Skills are always changing
For the latest information about this skill visit CNC Turning on worldskills.org.
CNC Turning
Creating prototypes from technical designs using a computer controlled lathe that cuts to ultra-fine specifications.
Why is this skill important?
CNC Machining has become one of the most important current machining processes in modern industry. Parts are made for household-equipment, telecommunications, cars, ships, aeroplanes, oil rigs, bridges, aerospace etc. Customers come from virtually every sector.
In CNC Machining the movements of the machine through computers and servomotors are dictated by the programmer. Once correctly programmed and set up, these machines can produce almost any shape and can repeat the process many times. This offers great advantages for quality and efficiency.
CNC Machining covers a broad variety of machining processes, such as grinding, welding, electrical discharging, milling and also turning.
Some may think that lathes (turning machines) are built to make round parts; however, CNC lathes are capable of producing almost any shape and any part.
Every customer has different requirements and demands and therefore each part is made of different materials, and needs different geometries, dimensions and surface qualities. To explain all the desired requirements to the machinist, the customer produces a technical drawing.
Machining starts with deciding how best to produce the part. There are many ways of doing this, like welding, milling, casting, and 3D Printing. One very important method is CNC Turning.
A CNC lathe is a very accurate computer-driven machine, where cutting tools, controlled by a program, are moved to cut away excessive material to result in the expected customer part. The CNC Turning machinist receives the technical drawing and uses the lathe in many ways to find solutions to build the part. These machines are very expensive, because they can do remarkable things. To have an idea of this, think what it means to achieve accuracy below ten microns, which is six to10 times thinner than a human hair.
The CNC Turning machinist uses a computer to tell the lathe how to move the tools and cut the part to the desired shape. They must also set up the lathe with all the necessary clamping devices, support devices, and cutting tools. These tools can cut almost every material (stainless steel, plastic, soft steel, aluminium, bronze, and so on). But the machinist has to choose well to avoid temperature variations, tool wear or vibration. Those factors influence the product and it can result in poor quality.
When the machine starts cutting material, the machinist makes sure that the dimensions exactly fit the customer specifications. For this, very accurate inspection tools are used. Once the machine is set up, the CNC-Turning machinist also monitors and optimizes the processes, to achieve even faster and better results for all the following parts.
Results
See all resultsRank | Medal | Result | Competitor | Country/Region |
---|---|---|---|---|
1. |
Gold |
760 |
Hongyu Wu |
China |
2. |
Silver |
748 |
Nguyen Xuan Thai |
Vietnam |
2. |
Silver |
746 |
Natthawut Phetngam |
Thailand |
2. |
Silver |
746 |
Hayato Shiozawa |
Japan |
5. |
Medallion for Excellence |
732 |
Minjun Shin |
Korea |
6. |
Medallion for Excellence |
719 |
Nicolas SCHWING |
France |
7. |
Medallion for Excellence |
715 |
Kevin Emhofer |
Austria |
8. |
Medallion for Excellence |
709 |
Hanan Alshamsi |
United Arab Emirates |
9. |
Medallion for Excellence |
704 |
Sander Hem Münchow |
Denmark |
10. |
Medallion for Excellence |
701 |
XUAN-ROU WANG |
Chinese Taipei |
11. | 699 |
Fabian Leuenberger |
Switzerland | |
12. | 691 |
Hannu Helve |
Finland | |
13. | 689 |
Christian Armando Rodriguez Montezco |
Mexico | |
14. | 683 |
Satyaranjan Mohanty |
India | |
15. | 681 |
Merle Ruffing |
Germany | |
16. | 679 |
Bun Long Chan |
Singapore | |
17. | 673 |
Alexander Johnsson |
Sweden | |
18. | 668 |
Ochbaatar Gankhuu |
Mongolia | |
19. | 656 |
Maxwell Melling |
Canada | |
20. | 652 |
Ilsur Tukayev |
Kazakhstan | |
Competitors
Hanan Alshamsi
United Arab Emirates
Bun Long Chan
Singapore
Kevin Emhofer
Austria
Ochbaatar Gankhuu
Mongolia
Hannu Helve
Finland
Alexander Johnsson
Sweden
Fabian Leuenberger
Switzerland
Maxwell Melling
Canada
Satyaranjan Mohanty
India
Sander Hem Münchow
Denmark
Natthawut Phetngam
Thailand
Christian Armando Rodriguez Montezco
Mexico
Merle Ruffing
Germany
Nicolas SCHWING
France
Minjun Shin
Korea
Hayato Shiozawa
Japan
Ilsur Tukayev
Kazakhstan
XUAN-ROU WANG
Chinese Taipei
Hongyu Wu
China
Nguyen Xuan Thai
Vietnam
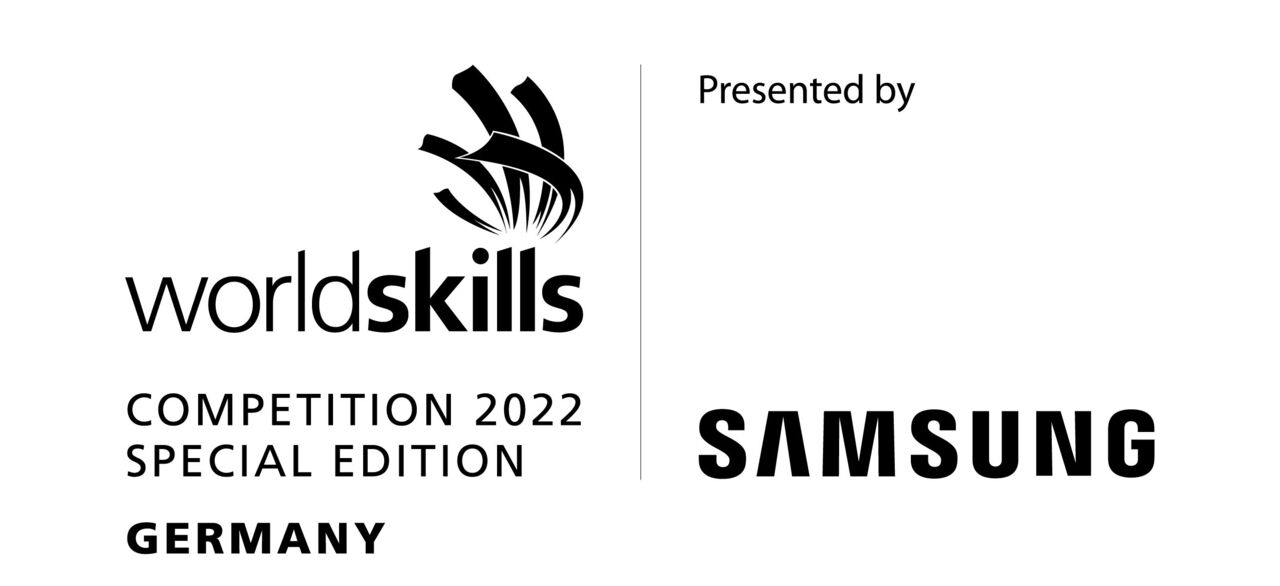
Hosting Partner

Gold Partners

Silver Partners

Bronze Partners

Government Funding
